Resource library
Access case studies, white paper, magazines, podcasts, videos and more.
Filters
{count} items
Resource type
Corporate/division
Business
Industry
Solutions by ecosystem
Capability
Product
Language
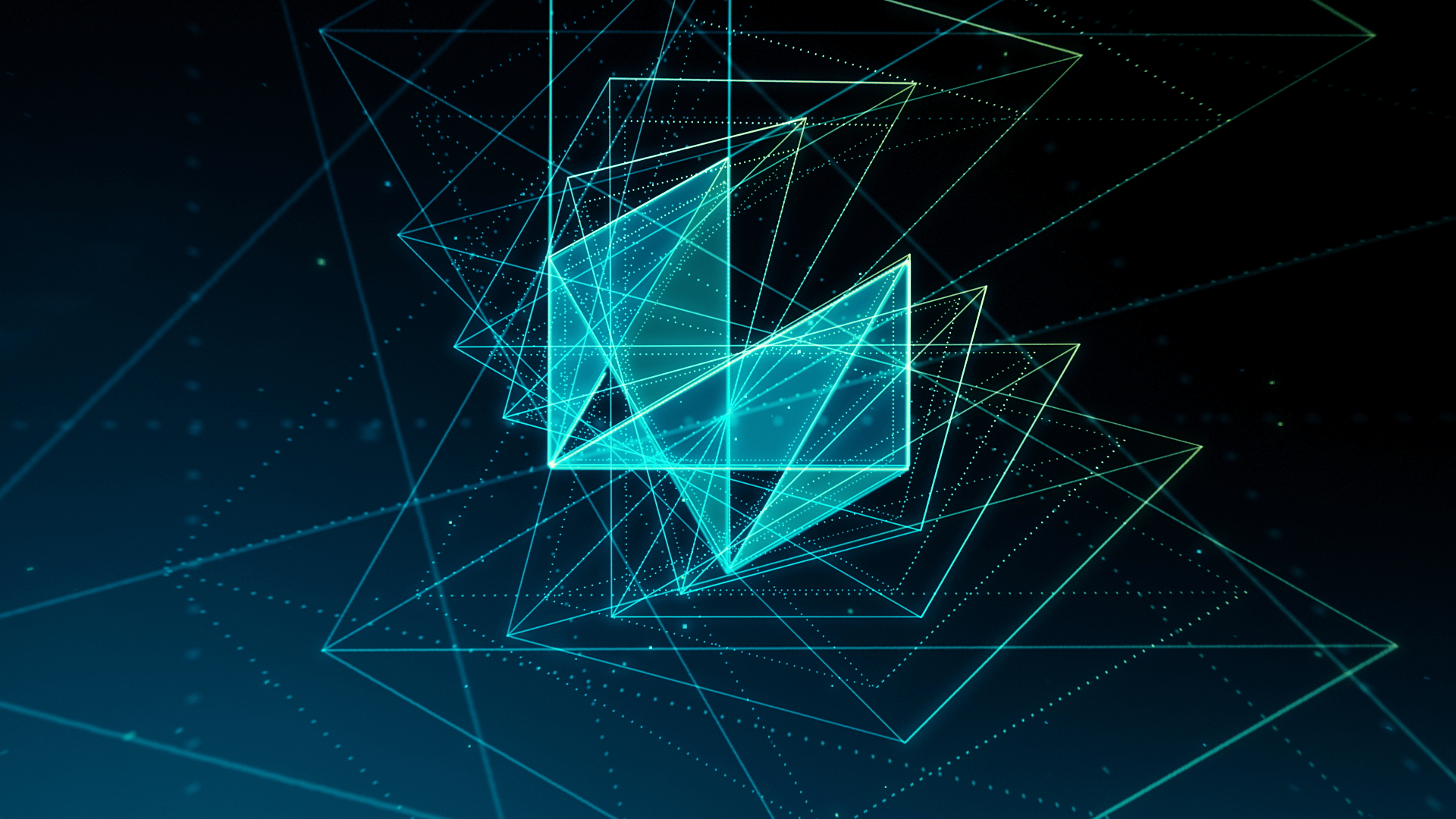